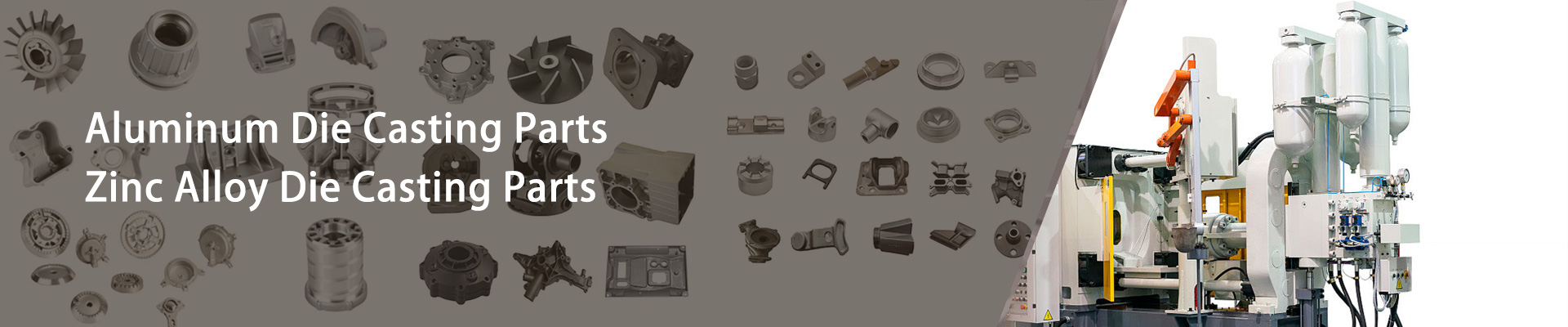
Construção Estrutural e Projeto de Sinergia Leve
2023-12-18 05:15
Projetistas e especialistas em fabricação geralmente apresentam disparidades significativas em seus objetivos, e isso é particularmente pronunciado na tecnologia de fundição. Tomando a junta de direção como exemplo, este artigo demonstra o potencial do desenvolvimento de componentes digitais para desenvolvedores e empresas.
Os projetistas buscam componentes com máxima leveza e estruturas de alta resistência, enquanto os especialistas em fundição devem garantir que os componentes sejam preenchidos sequencialmente de forma adequada, otimizando o sistema de fundição para ser o mais simplificado possível e evitando porosidade interna ou vazios de solidificação. Alcançar um compromisso entre estes objectivos normalmente envolve múltiplas rondas de ajustamentos, prolongando o processo de desenvolvimento.
Além disso, esses ajustes exigem a aplicação de conhecimentos profissionais acumulados ao longo dos anos. A colaboração entre o fornecedor automotivo internacional Elise GmbH e a Universidade de Kassel revela que a utilização da plataforma de software ELISE pode melhorar significativamente a automação de tais processos de desenvolvimento.
Ajustes de Design Adaptativo
A interconexão digital de CAD, otimização de topologia, análise de P&D e ferramentas de simulação de processos acelera o processo de fabricação de componentes fundidos, um aspecto crucial do futuro desenvolvimento eficiente de produtos. Os engenheiros desenvolveram um método usando o software ELISE, combinando o software de otimização de topologia Altair-Optistruct da Altair e o Magma V5 da Magmasoft GmbH, para encontrar uma solução de projeto semiautomática sinérgica e otimizada (Figura 1). Essas soluções atendem não apenas aos requisitos do processo de produção de fundição, mas também aos requisitos estruturais dos componentes.
Neste cenário, a funcionalidade de projeto digital do ELSE é empregada para detectar e prevenir o acúmulo de material durante o processo de fundição. Dados como forma, volume e posição de nós térmicos maiores são inseridos em funções desenvolvidas, onde esses dados são resultados simulados por meio de otimização topológica no Magmasoft. Podem ser previstos problemas crescentes no processo de produção e aplicações subsequentes na área de solidificação.
Além disso, o tempo de solidificação do material é usado para determinar automaticamente a direção de solidificação e ajustar as áreas de fundição afetadas. Para melhorar a moldabilidade, o software ELISE engrossa o bolo de forma adaptativa e penetra em estruturas de componentes mais profundas. Na segunda etapa, identifica caminhos de nós térmicos detectados na direção de solidificação.
Exemplo de aplicação
Num estudo digital específico, foi desenvolvida a manga de eixo dianteira. A otimização da topologia considerou parâmetros cruciais de fabricação, como direção de desmoldagem e espessura mínima da parede. A otimização baseou-se em três condições de carga rígidas simplificadas, especificamente concebidas para suportar a carga da parte superior da manga de eixo dianteira. Conflitos entre rigidez e solidificação direcional normalmente ocorrem na região do pescoço de ganso (Figura 2).
Depois de concluir a otimização da topologia, a suavização da peça e sua transformação novamente em um projeto moldável foram obtidas usando o ELISE. Neste cenário, as limitações do espaço de projeto foram consideradas e o modelo computacional ajustado de acordo. Os resultados servem como protótipos de validação de P&D e espaços em branco para simulação de fundição, eliminando a demorada etapa de redesenhar a estrutura do projeto da topologia. Outra vantagem deste método é a eliminação da necessidade de fabricação de novos modelos para cada iteração de simulação de fundição.
Otimização
A junta de direção acima exibe três nós térmicos de solidificação significativos, com a solidificação ocorrendo em ambos os lados do canal de entrada ou canal interno. Agora, esses resultados são exportados do programa Magmasoft em diferentes etapas de tempo e posteriormente processados usando o método de otimização de fundição desenvolvido. A partir daqui, fica evidente como foram feitos ajustes em áreas relevantes para obter melhores efeitos de solidificação direcional (Figura 3). No componente não otimizado (Figura 3a), a área de solidificação formada não pode ser alimentada para baixo, resultando na formação de um nó térmico que leva à porosidade. Ao engrossar a junta de direção durante o processo de solidificação (Figura 3b), o controle foi exercido, evitando a formação de áreas de solidificação, evitando a formação de nós térmicos e reduzindo ou evitando completamente a geração de poros.
Os componentes otimizados desta forma podem ser fundidos de uma maneira mais simples e estável. Todos os principais nós térmicos são reduzidos, ou mesmo totalmente evitados (Figura 4).
A taxa de porosidade prevista resultante desta abordagem também apresenta uma melhoria significativa. Além disso, a análise de desempenho indica ainda que o componente excede os requisitos, atendendo a três condições de carga rígida especificadas, proporcionando espaço para redução de peso.
Conclusão
A utilização do design digital no processo de desenvolvimento é o primeiro passo para a automação do desenvolvimento de componentes fundidos. Essa tecnologia reduz o trabalho manual tradicionalmente empregado pelos engenheiros de desenvolvimento em iterações comuns, proporcionando liberdade adicional para atividades criativas e de valor agregado. Injeta nova vitalidade nos processos de engenharia e negócios de desenvolvimento de produtos, acelerando o processo de inovação e fortalecendo vantagens competitivas.
Obter o preço mais recente? Responderemos o mais breve possível (dentro de 12 horas)